What to do if internal carbonization occurs in stainless steel reactor? How to deal with carbonized materials in stainless steel reactor?
Stainless steel reactor as a very precise equipment, its technical content is very high, so people like to use it in some fine reactions and harsh reaction conditions.
In recent years, stainless steel reactor is more and more widely used. In order to avoid the solid reaction material precipitated to the bottom of stainless steel reaction tank, a new stainless steel reactor came into being.
Based on the basic design and heating mode of the original stainless steel reactor, some adjustments have been made to the bottom of the stainless steel reactor. A good solution to such a problem, the next small editor to take you to understand.
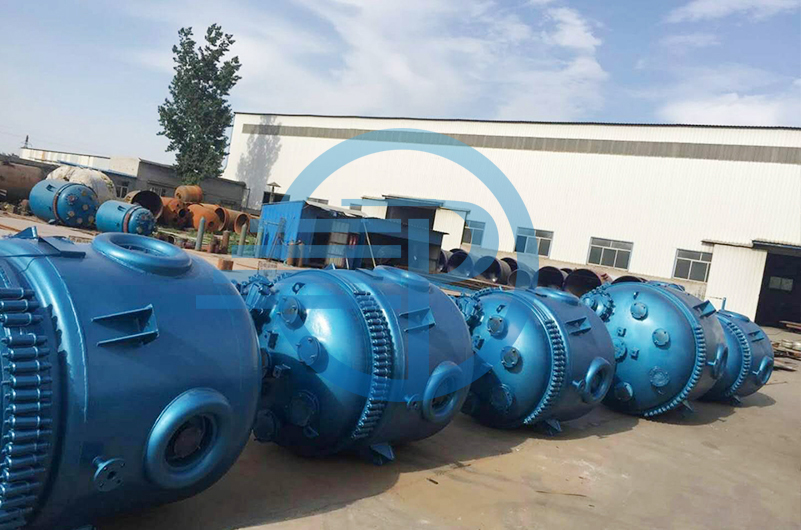
Because all the problems are due to the solid reaction materials precipitated to the bottom of stainless steel reaction tank. The main solution is to avoid sedimentation even without mixing or stirring. The auxiliary reaction can be achieved by adding 3 cm of stainless steel at the bottom of the furnace, which is slightly higher than the actual reaction of stainless steel.
In this way, the solid reactants will precipitate on the bottom of the auxiliary stainless steel reaction vessel, instead of forming an insulation layer on the actual stainless steel reactor bottom. Through the convection between the bottom gaps of stainless steel reaction vessels, the heat transfer will be continuous and uniform.
The stainless steel screen with small diameter (ss314) on the bottom of the reactor is made of stainless steel, which has a smaller diameter than stainless steel. When the solid reaction material load is very heavy, a metal ring can be added under the auxiliary bottom as a support. In this way, the concentration of solid materials at the bottom of stainless steel reactor can be avoided.